Understanding Porosity in Welding: Checking Out Reasons, Results, and Avoidance Methods
Porosity in welding is a persistent difficulty that can significantly affect the high quality and stability of welds. As experts in the welding sector are aware, comprehending the reasons, results, and prevention strategies connected to porosity is vital for accomplishing robust and dependable welds. By diving right into the source of porosity, examining its destructive effects on weld quality, and exploring effective prevention methods, welders can boost their knowledge and skills to generate premium welds constantly. The intricate interaction of elements contributing to porosity requires a comprehensive understanding and an aggressive strategy to make certain effective welding outcomes.
Usual Root Causes Of Porosity
Contamination, in the form of dust, oil, or corrosion on the welding surface area, creates gas pockets when warmed, leading to porosity in the weld. Improper protecting happens when the securing gas, commonly used in processes like MIG and TIG welding, is not able to fully safeguard the molten weld pool from reacting with the surrounding air, resulting in gas entrapment and subsequent porosity. In addition, poor gas insurance coverage, frequently due to inaccurate circulation rates or nozzle positioning, can leave parts of the weld vulnerable, enabling porosity to develop.
Effects on Weld Quality
The existence of porosity in a weld can significantly compromise the general quality and honesty of the bonded joint. Porosity within a weld develops spaces or dental caries that compromise the framework, making it much more prone to cracking, rust, and mechanical failing. These voids act as tension concentrators, decreasing the load-bearing capability of the weld and raising the probability of early failure under applied tension. Additionally, porosity can also function as possible sites for hydrogen entrapment, more aggravating the deterioration of the weld's mechanical buildings.
In addition, porosity can impede the efficiency of non-destructive screening (NDT) strategies, making it challenging to discover various other defects or gaps within the weld. This can lead to substantial security issues, specifically in important applications where the structural stability of the welded elements is critical.
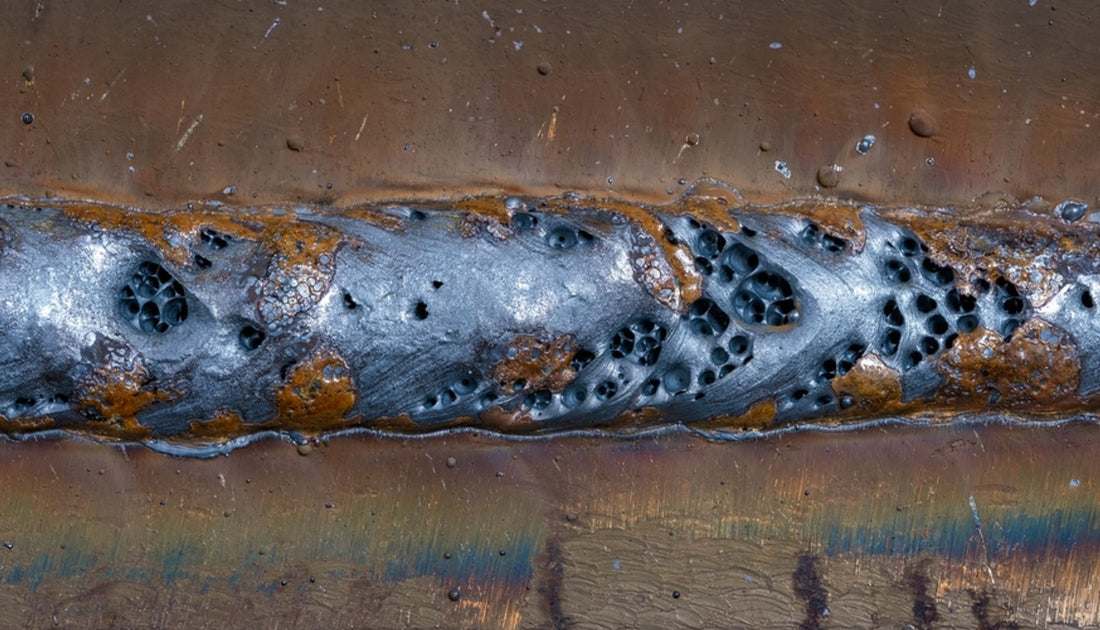
Prevention Techniques Introduction
Provided the destructive influence of porosity on weld quality, efficient avoidance methods are vital to maintaining the architectural honesty of welded joints. Furthermore, picking the ideal welding article source specifications, such as voltage, existing, and take a trip rate, can help decrease the risk of porosity development. By including these avoidance methods right into welding techniques, the event of porosity can be considerably reduced, leading to more powerful and much more reliable home bonded joints.
Value of Correct Protecting
Appropriate securing in welding plays an important function in stopping climatic contamination and guaranteeing the honesty of bonded joints. Securing gases, such as argon, helium, or a mixture of both, are commonly made use of to secure the weld swimming pool from reacting with aspects in the air like oxygen and nitrogen. When these responsive components come into call with the hot weld swimming pool, they can trigger porosity, bring about weak welds with reduced mechanical buildings.

Insufficient protecting can cause various issues like porosity, more helpful hints spatter, and oxidation, compromising the structural stability of the bonded joint. Sticking to proper protecting methods is necessary to produce top notch welds with very little issues and guarantee the longevity and dependability of the welded parts.
Monitoring and Control Methods
Exactly how can welders successfully keep an eye on and regulate the welding procedure to guarantee optimal results and stop flaws like porosity? One secret method is via using innovative monitoring technologies. These can consist of real-time tracking systems that provide comments on specifications such as voltage, existing, travel rate, and gas circulation prices. By continuously keeping an eye on these variables, welders can identify deviations from the suitable conditions and make immediate modifications to prevent porosity development.

In addition, applying correct training programs for welders is important for monitoring and regulating the welding procedure effectively. What is Porosity. Educating welders on the relevance of maintaining constant parameters, such as correct gas shielding and take a trip speed, can help avoid porosity concerns. Regular analyses and qualifications can additionally make certain that welders excel in tracking and controlling welding processes
In addition, the use of automated welding systems can boost surveillance and control abilities. These systems can exactly manage welding specifications, decreasing the chance of human mistake and guaranteeing regular weld top quality. By integrating sophisticated tracking innovations, training programs, and automated systems, welders can effectively keep an eye on and manage the welding procedure to reduce porosity defects and achieve top quality welds.
Verdict
Comments on “What is Porosity in Welding: Usual Resources and Efficient Remedies”